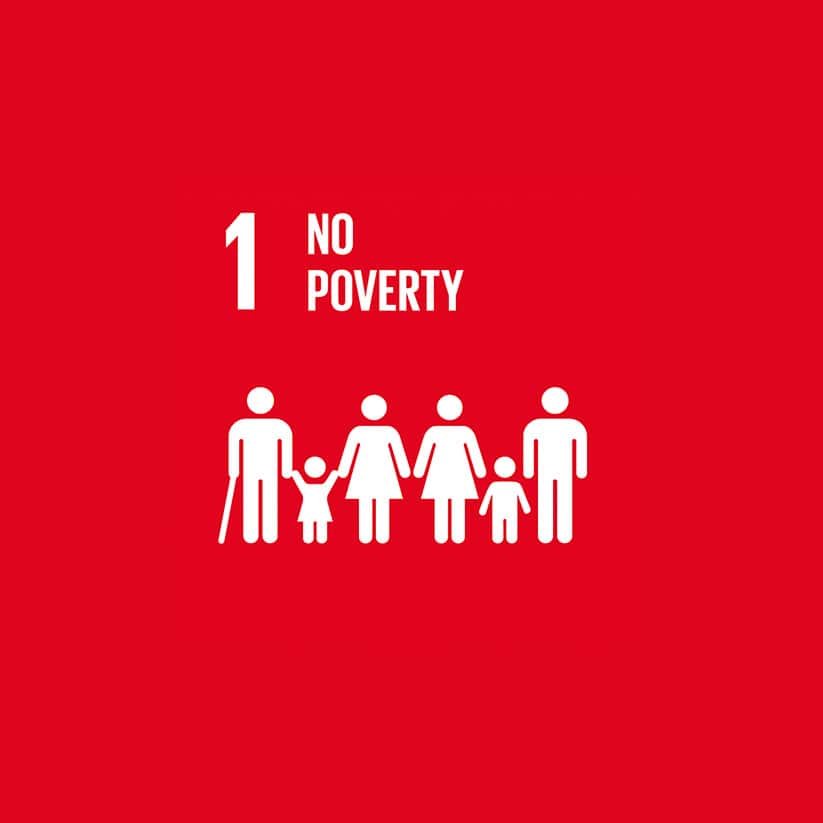
InQuik’s modular engineering is transforming bridge construction, providing a much more sustainable approach to one of the world’s most common infrastructure needs.
“When we were developing the InQuik technology, we had ease of construction and sustainability front of mind, which means we developed a system that was easy to install and had massive longevity,” says Ben Mullaney, InQuik’s Chief Technology and Innovation Officer.
Prefabricated sections made in a factory – from the supporting abutments to the barriers for each side and the surface decks – are assembled on site. Concrete is then poured into the steel-reinforced module, which sets to create a robust, fully integral structure.
The procedure is simple and fast. And the steel weathers to a natural, aesthetically pleasing finish while protecting the concrete from corrosion.
Murphy’s Bridge, across the Tuross River in rural New South Wales, Australia, is a compelling example of the transformative effect InQuik technology can have on a community.
In 2019, a devastating bush fire destroyed the original bridge, stranding the small town of Cadgee. To avoid a time-consuming and costly 64km detour, locals resorted to crossing the river by kayak – a risky proposition in the flood-prone waters.
InQuik’s replacement bridge resulted in a far more resilient and sustainable structure. Due to the nature of its modular design, the bridge was constructed using local plant, materials, and labor. It requires minimal maintenance, with a design life of at least 100 years – newer InQuik bridges actually push that even further to 150 years.
Cadgee resident Sharon Harris sums up the impact the new bridge had on the town: “Once the bridge reopened, it gave us back the total joy of communication and gatherings.”
Founded in 2017, InQuik is based in Pyrmont, New South Wales, and has delivered more than 200 bridges across Australia, the Pacific, and the US. The company is looking to build on this success by bringing its unique bridge technology to the European market.
InQuik’s completed bridge projects show how modules can be configured as single- or multi-span bridges covering a range of lengths can be placed side by side to achieve the required number of lanes.
Compared to alternative bridge construction methods such as precast or conventional in situ bridges, InQuik’s lightweight and long-lasting bridge system reduces the cost of on-site labor, is easier to transport, and more sustainable. The efficient and straightforward assembly also results in less exposure to risk for the workforce.
InQuik is redefining construction by extending its methods to rail bridges, commercial and industrial buildings, and maritime structures. Built with InQuik’s proven technology, these projects will continue to connect and support local communities such as Murphy’s Bridge.
“What I get most passionate about with InQuik is the fact that we have a big impact on people’s lives,” says Mullaney.
The company’s pioneering engineering projects align with SDG 9, which aims to build resilient infrastructure, promote inclusive and sustainable industrialization, and foster innovation.
Lightweight and prefabricated, InQuik bridges typically take only three to five days to install.