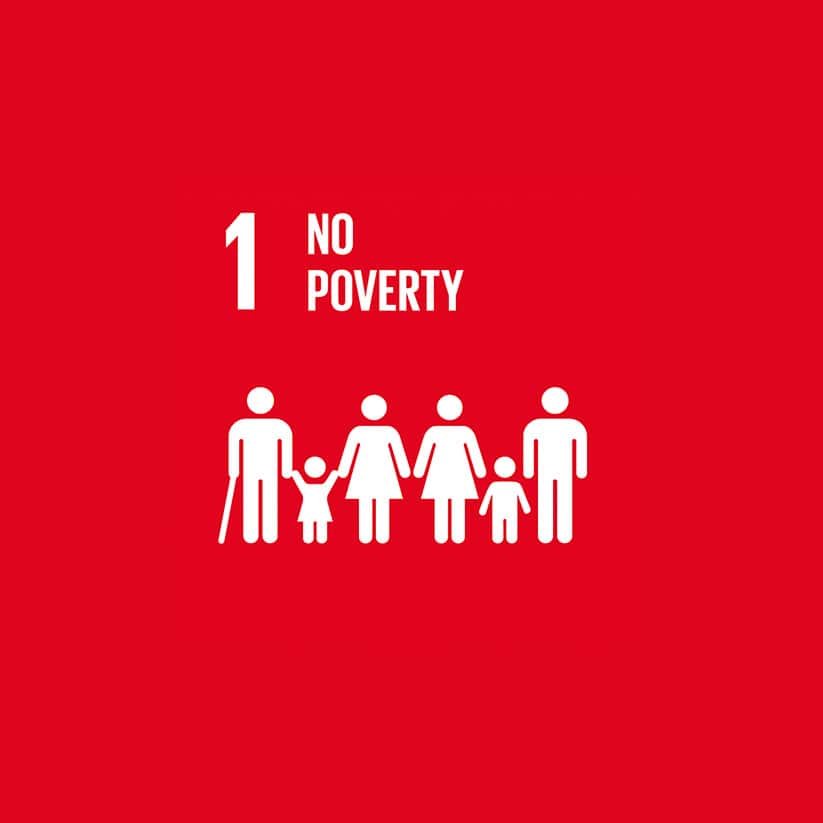
Albany International has a proud history of innovation. This dates back to 1895, when the company began making “machine clothing” – custom-designed, woven industrial belts for the machines that make paper and paperboard products.
In the late 1990s, the company branched into the engineered composites sector and started weaving textiles for composites in the aerospace industry. In doing so, it pioneered high-precision, 3D weaving looms that were not commercially available at the time.
“We are expert weavers. And we’ve brought this skill to the next level with 3D weaving,” says Robert A. Hansen, Senior Vice President and Chief Technology Officer at Albany International.
Through these two distinct yet intimately connected businesses, Albany Machine Clothing and Albany Engineered Composites, Albany International is using the science and craft of weaving to design and manufacture the sustainable products that are reshaping the world today.
“Change is coming to the aerospace industry, and we are at the forefront of that change,” says Hansen.
The future of commercial aerospace depends on making the sector vastly more sustainable, and Albany International’s engineered materials are proving transformational in this sphere. From jet fan casings and the fan blades themselves, to fuselage frames and landing gear struts, the company’s composite components have a high strength-to-weight ratio, which saves fuel and enhances performance.
In addition to conventional aerospace, Albany International is developing materials for entirely new types of aircraft in the emerging advanced air mobility sector. Electric vertical takeoff and landing (eVTOL) planes are destined to revolutionize urban travel.
“As we develop better, stronger, and ever-lighter 3D woven materials, we’re working towards the next generation of all-composite aircraft that will be far more efficient and sustainable than today’s planes.”
Albany International is headquartered in the US, in Rochester, New Hampshire. It employs 5,400 people worldwide in 30 locations across 13 countries, with European manufacturing sites in Belgium, England, France, Germany, Italy, Spain, and Sweden.
Through Albany International’s dedication to materials science and R&D, the company hopes to inspire customers to improve their own performance and sustainability goals, “whether it’s helping machine clothing customers use less energy and less water in the process or it’s contributing to lighter, more durable aircraft engines that are 15% more fuel efficient,” says Sofi Karlsson, R&D Manager, Albany International.
For Albany International, innovation is at the heart of a more sustainable aerospace future, with the application of materials and expertise that enables aircraft to fly further and longer than ever before.
“It was innovation that got us into the aerospace business, and it’s innovation that will help our customers build the next generation of more sustainable aircraft,” says Hansen.
With 130 years of innovation under its belt, Albany International is committed to SDG 9, which aims to build resilient infrastructure, promote inclusive and sustainable industrialization, and foster innovation.
Albany International’s most complex 3D weaving looms are fed by more than 2,000 spools of carbon-fiber filaments, known in the textile industry as “tows”.